プレス機の設備保全
課題
高張力鋼板のピアシング工程のプレスがよく故障する
- プレスの故障が頻繁に起きるため、成形速度を下げているが故障頻度はほぼ横ばい
- 生産量は低下し、生産計画も乱れがちになっている
- プレスの修繕費が嵩む上、トラブル対応の人件費も増加している
解決策
プレスのコネクティングロッド部の6本のボルトのうち、2本を圧電式荷重センサー「PiezoBolt」に付け替えて、成形時の荷重変動をモニタリングしました。
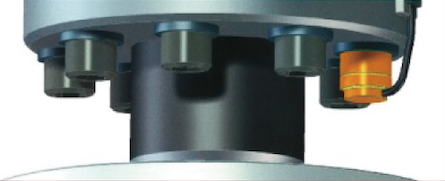
その結果、80SPMの条件下では、ブレークスルー現象が発生していたが、120SPMでは最小限に抑えられていることが分かりました。また、120SPMでは全体の荷重負荷も37%低減することが分かったため、生産速度を120SPMに変更。これによってプレス機への負担は低減し、プレス機の故障頻度は確実に減少しました。
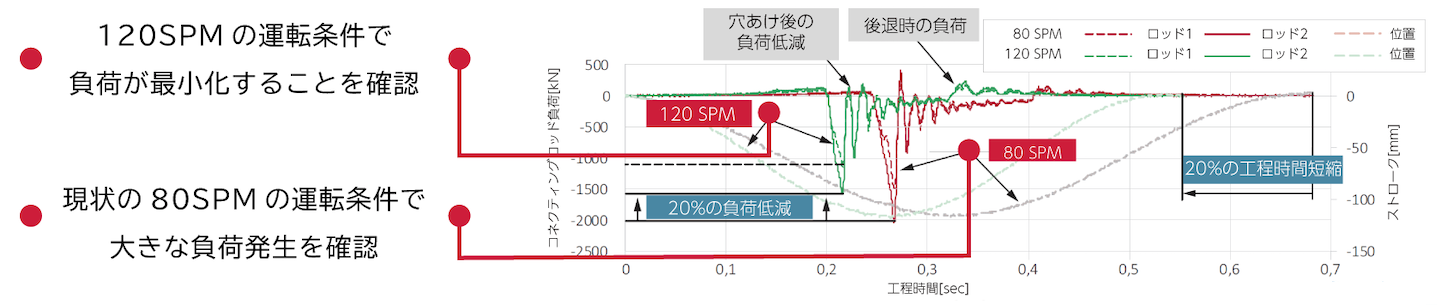
結果
成形条件の最適化で、プレス機の故障頻度を減少
- 故障原因となる原因を特定し、設備の負担ができるだけ少ない成形を実施できるようになった
- 故障の発生による修理費や人件費の削減を実現することができた
- プレス設備事態の負荷状態だけでなく、製品の不具合が出る原因についても計測結果により考察できるようになった
お客様の声
プレス成形でショットごとに荷重の変化がリアルタイムでモニタリングできることでプレス設備の状態が随時確認可能な点に魅力を感じた。ボルト型であるため、プレス設備のあらゆる場所に締結ができ、今後様々な課題に活かすことができると思った。
事例一覧